Hydraulic hoses are key components for transmitting power in hydraulic systems and are widely used in engineering machinery, mining equipment, agricultural machinery and other fields. Their performance directly affects the safety, reliability and service life of the system. In order to meet the needs of different working conditions, hydraulic hoses present a variety of classifications in structure, material and performance, and follow strict implementation standards. The following will systematically introduce the technical characteristics and application specifications of hydraulic hoses from the two aspects of classification and implementation standards.
1. Classification of hydraulic hoses
Hydraulic hoses can be classified according to structure, purpose and working pressure to meet the needs of different scenarios.
Classification by structure:
- Wire braided hose: It consists of an inner rubber layer, a wire braided reinforcement layer and an outer rubber layer. It has high pressure resistance and is suitable for medium and high pressure hydraulic systems. It is characterized by good flexibility and is suitable for occasions that require frequent bending.
- Wire wound hose: It is composed of an inner rubber layer, a multi-layer wire wound reinforcement layer and an outer rubber layer. It has higher pressure resistance and is suitable for high-pressure and ultra-high-pressure hydraulic systems. It is characterized by strong pressure bearing capacity, but a large bending radius.
- Fiber reinforced hose: It is composed of an inner rubber layer, a fiber reinforcement layer and an outer rubber layer, and is suitable for low-pressure hydraulic systems. It is characterized by light weight and low cost, but weak pressure resistance.
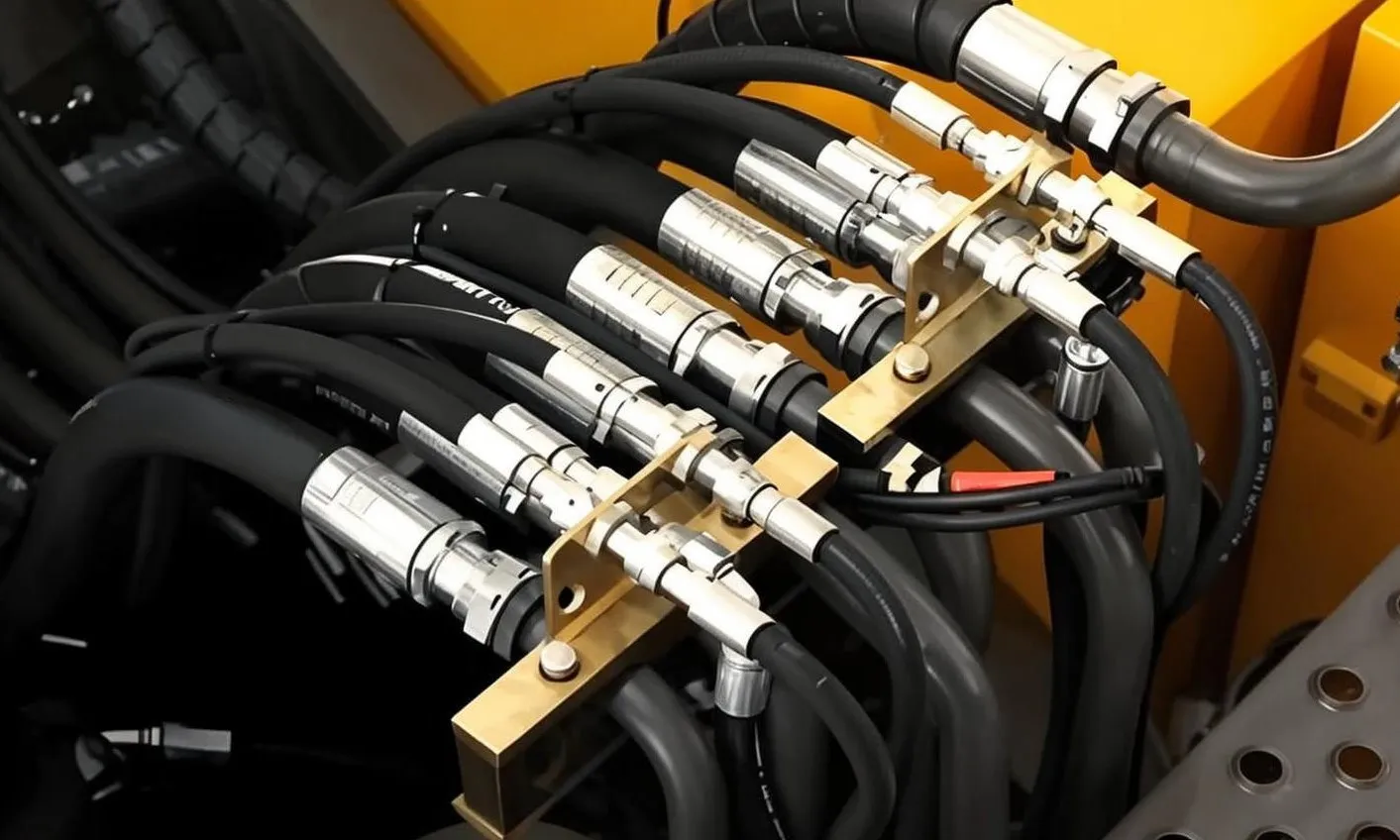
Classification by use:
- General hydraulic hose: It is suitable for hydraulic systems of general industrial equipment and has good comprehensive performance.
- Oil-resistant hydraulic hose: It is made of oil-resistant rubber material and is suitable for hydraulic systems in contact with oil media.
- High temperature resistant hydraulic hose: It is made of high temperature resistant rubber material and is suitable for hydraulic systems in high temperature environments.
- Corrosion-resistant hydraulic hose: It is made of special rubber or synthetic materials and is suitable for hydraulic systems with corrosive media.
Classification by working pressure:
- Low-pressure hose: Working pressure below 10MPa, suitable for light equipment.
- Medium-pressure hose: Working pressure between 10-30MPa, suitable for medium-sized equipment.
- High-pressure hose: Working pressure between 30-60MPa, suitable for heavy equipment.
- Ultra-high-pressure hose: Working pressure above 60MPa, suitable for special working conditions.
2. Implementation standards of hydraulic hoses
The production and use of hydraulic hoses must comply with international, national and industry standards to ensure their performance and quality.
International standards:
- ISO 18752: It specifies the size, performance and test methods of hydraulic hoses and is a widely recognized standard worldwide.
- SAE J517: Developed by the American Society of Automotive Engineers, it is suitable for hydraulic hoses in the automotive and engineering machinery fields.
National Standard:
- GB/T 3683: Chinese national standard, which specifies the technical requirements and test methods of hydraulic hoses and is the main basis for domestic production and use.
- GB/T 10544: Applicable to wire-wound hydraulic hoses, which specifies their design, manufacturing and inspection requirements in detail.
Industry Standard:
- DIN 20023: German industrial standard, applicable to the design and manufacture of hydraulic hoses, known for its rigor and high requirements.
- EN 856: European standard, applicable to high-pressure hydraulic hoses, widely used in the European market.
3. Selection and application of hydraulic hoses
In actual applications, the selection of hydraulic hoses needs to comprehensively consider factors such as working pressure, medium type, ambient temperature and bending radius. For example, wire-wound hoses should be used in high-pressure systems, while corrosion-resistant hoses should be selected in corrosive environments. In addition, the following points should be noted during installation and use:
Correct installation: Avoid excessive bending or twisting to ensure that the hose is firmly connected to the joint.
Regular inspection: Check whether there are cracks, wear or bulges on the surface of the hose, and replace the damaged hose in time.
Follow the standards: Strictly select, install and maintain in accordance with relevant standards to ensure the safety and reliability of the system.
The classification and implementation standards of hydraulic hoses are important bases for ensuring their performance and quality. Through scientific classification and strict compliance with standards, the operating efficiency and safety of the hydraulic system can be effectively improved. In the future, with the advancement of material technology and manufacturing processes, hydraulic hoses will develop towards higher performance, longer life and more environmental protection, providing more reliable solutions for the industrial field.
Hydraulic hoses are key components for transmitting power in hydraulic systems and are widely used in engineering machinery, mining equipment, agricultural machinery and other fields. Their performance directly affects the safety, reliability and service life of the system. In order to meet the needs of different working conditions, hydraulic hoses present a variety of classifications in structure, material and performance, and follow strict implementation standards. The following will systematically introduce the technical characteristics and application specifications of hydraulic hoses from the two aspects of classification and implementation standards.
1. Classification of hydraulic hoses
Hydraulic hoses can be classified according to structure, purpose and working pressure to meet the needs of different scenarios.
Classification by structure:
- Wire braided hose: It consists of an inner rubber layer, a wire braided reinforcement layer and an outer rubber layer. It has high pressure resistance and is suitable for medium and high pressure hydraulic systems. It is characterized by good flexibility and is suitable for occasions that require frequent bending.
- Wire wound hose: It is composed of an inner rubber layer, a multi-layer wire wound reinforcement layer and an outer rubber layer. It has higher pressure resistance and is suitable for high-pressure and ultra-high-pressure hydraulic systems. It is characterized by strong pressure bearing capacity, but a large bending radius.
- Fiber reinforced hose: It is composed of an inner rubber layer, a fiber reinforcement layer and an outer rubber layer, and is suitable for low-pressure hydraulic systems. It is characterized by light weight and low cost, but weak pressure resistance.
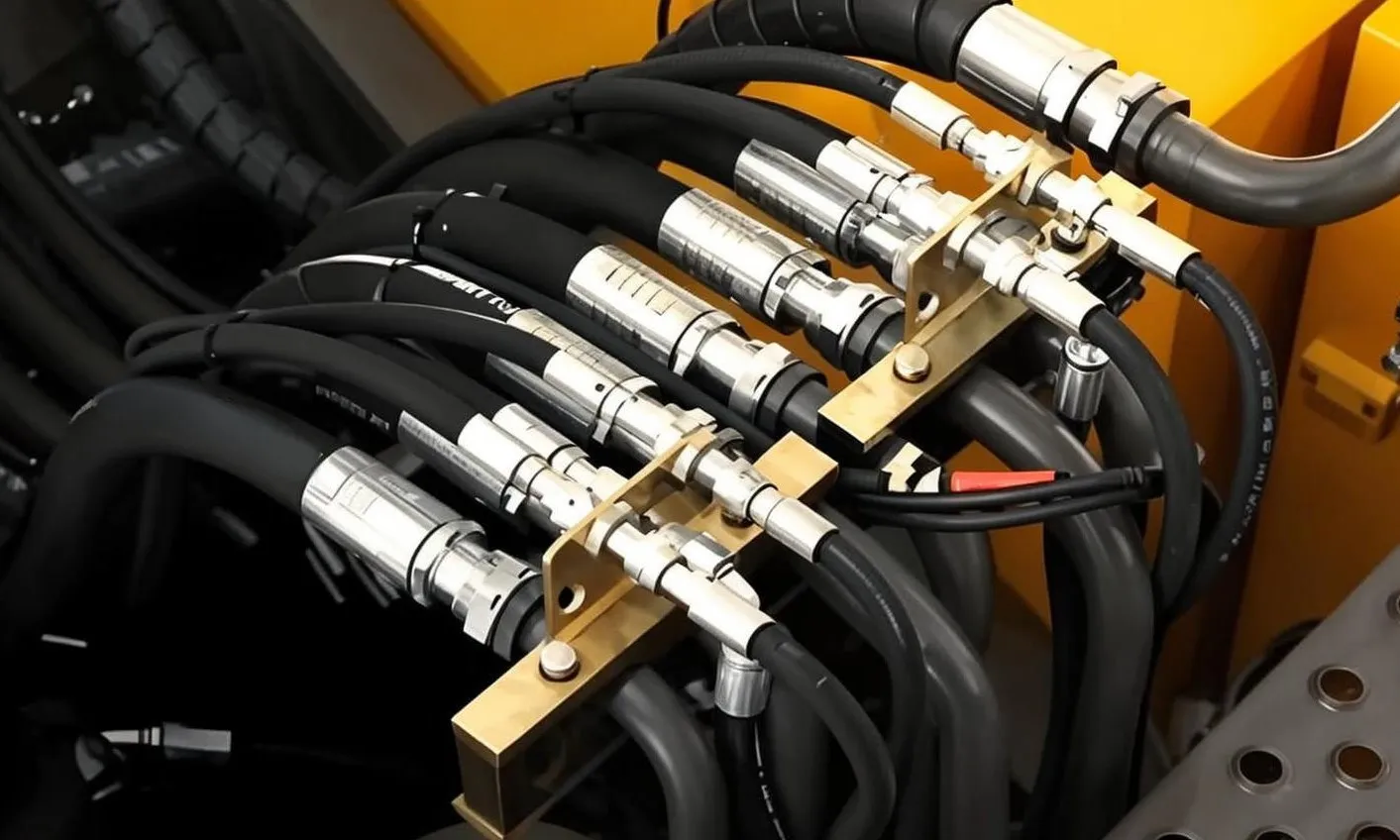
Classification by use:
- General hydraulic hose: It is suitable for hydraulic systems of general industrial equipment and has good comprehensive performance.
- Oil-resistant hydraulic hose: It is made of oil-resistant rubber material and is suitable for hydraulic systems in contact with oil media.
- High temperature resistant hydraulic hose: It is made of high temperature resistant rubber material and is suitable for hydraulic systems in high temperature environments.
- Corrosion-resistant hydraulic hose: It is made of special rubber or synthetic materials and is suitable for hydraulic systems with corrosive media.
Classification by working pressure:
- Low-pressure hose: Working pressure below 10MPa, suitable for light equipment.
- Medium-pressure hose: Working pressure between 10-30MPa, suitable for medium-sized equipment.
- High-pressure hose: Working pressure between 30-60MPa, suitable for heavy equipment.
- Ultra-high-pressure hose: Working pressure above 60MPa, suitable for special working conditions.
2. Implementation standards of hydraulic hoses
The production and use of hydraulic hoses must comply with international, national and industry standards to ensure their performance and quality.
International standards:
- ISO 18752: It specifies the size, performance and test methods of hydraulic hoses and is a widely recognized standard worldwide.
- SAE J517: Developed by the American Society of Automotive Engineers, it is suitable for hydraulic hoses in the automotive and engineering machinery fields.
National Standard:
- GB/T 3683: Chinese national standard, which specifies the technical requirements and test methods of hydraulic hoses and is the main basis for domestic production and use.
- GB/T 10544: Applicable to wire-wound hydraulic hoses, which specifies their design, manufacturing and inspection requirements in detail.
Industry Standard:
- DIN 20023: German industrial standard, applicable to the design and manufacture of hydraulic hoses, known for its rigor and high requirements.
- EN 856: European standard, applicable to high-pressure hydraulic hoses, widely used in the European market.
3. Selection and application of hydraulic hoses
In actual applications, the selection of hydraulic hoses needs to comprehensively consider factors such as working pressure, medium type, ambient temperature and bending radius. For example, wire-wound hoses should be used in high-pressure systems, while corrosion-resistant hoses should be selected in corrosive environments. In addition, the following points should be noted during installation and use:
Correct installation: Avoid excessive bending or twisting to ensure that the hose is firmly connected to the joint.
Regular inspection: Check whether there are cracks, wear or bulges on the surface of the hose, and replace the damaged hose in time.
Follow the standards: Strictly select, install and maintain in accordance with relevant standards to ensure the safety and reliability of the system.
The classification and implementation standards of hydraulic hoses are important bases for ensuring their performance and quality. Through scientific classification and strict compliance with standards, the operating efficiency and safety of the hydraulic system can be effectively improved. In the future, with the advancement of material technology and manufacturing processes, hydraulic hoses will develop towards higher performance, longer life and more environmental protection, providing more reliable solutions for the industrial field.